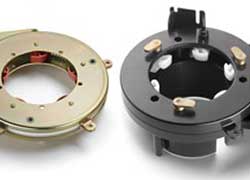
OPTIMIZING AND SAVING
Redesigning a metal product in plastic helps to:
- increaseefficiency and sturdiness;
- speed up assembly operations with significantreductions in maintenance costs;
- improve the appearance;
- achieve a significant reduction in the environmental impact.
This meat hook, which used to be made from shaped and welded stainless steel, is now manufactured using glass fibre-reinforced PA. It is much lighter, production times are reduced 50:1 and costs are equally reduced.
The material is recyclable and its food-contact conformity is certified.
This cup dispenser used to be made with mechanical technology from shaped, welded and painted sheet metal. The components were assembled and fastened using screws.
PlastDesignStudio redesigned it in plastic and optimized it for injection moulding production.
Eliminating all the parts in sheet metal resulted in optimization of assembly by means of interlocking parts, simplification of installation and maintenance, reductions in weight and noise emissions during operation.
The product turned out to be more eco-friendly thanks to the lack of paints used and the fully recyclable nature of the plastic components.
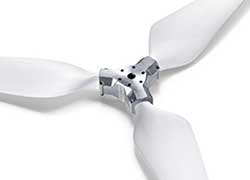
APPLYING NEW TECHNIQUES
Propeller for aeroplane with up to 100 hp engine power made by assembling 3 blades on an ergal boss.
The blades are injection moulded and hollowed out using gas injection technology
The thermostatic material used, produced exclusively for PlastDesignStudio and Csplast, is reinforced with carbon and aramid fibre to give the plastic lightness, a high tensile modulus and resistance to impact in the event of rain and hail.
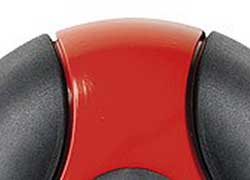
RUBBER/PLASTIC OVERMOULDING
Overmoulding makes it possible to mould certain rubber elements or details directly onto the plastic component. These rubber parts adhere perfectly to the part with no need for gluing or the manual insertion of other components.
This technique is used in the case of:
- aesthetic needs: for example to create products made up of different colours and materials and soft to the touch
- ergonomic needs: for example to make a non-slip hand grip to facilitate the use of hand-held devices and electronic equipment or to create bumpers or soft edges to protect objects from impact
- sealing and waterproofing needs: for example on parts which need to withstand high pressures or are exposed to the weather
- performance needs: for example to make parts which need to be resistant to critical temperatures or protected against chemical infiltrations.
overmoulding requires an initial injection of a material into a mould designed to create the component (or a part of it) and a second injection using a different materials (for example thermoplastic rubber) to complete the article.
Here is the latest creation by PlastDesignStudio in which overmoulding was used to make a rubber grip.
Other examples of products made using overmoulding: a drain ring for a shower plug hole and a toy
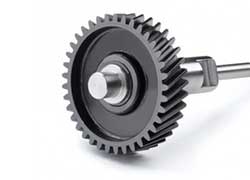
COMBINING DIFFERENT MATERIALS
When metal cannot be replaced, the solution is co-moulding using both plastic and metal.
This technique makes it possible to fully exploit the benefits of both materials by skilfully combining the two.
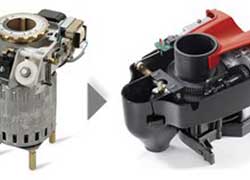
UPDATING COMPLEX MECHANISMS
Food grinder unit, for over thirty years manufactured using mechanical technology: casting, milling, drilling threading, assembly.
Materials used: steel, aluminium, brass.
New grinding unit redesigned for production using technopolymer injection moulding: the use of this technique significantly reduces the weight of the unit and number of components thus speeding up assembly times.
The materials used are 100% recyclable.
All of this translates into a significant reduction in costs.
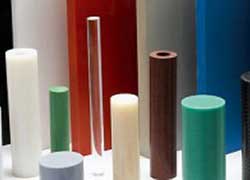
WHICH MATERIAL FOR YOUR PRODUCT?
In PlastDesignStudio each project starts off with a careful analysis of the client’s requirements and the requisites the item must have.
Our in-depth knowledge of the potentials offered by the types of polymers available on a constantly evolving market allows us to help you select the perfect material.
You may find that an article which up until yesterday was made using metal materials is much more efficient and economical when made using a technopolymer. The technologies we have allow us to analyse a problem and find a solution, adopting quick, versatile and economic systems for the experimentation stages.
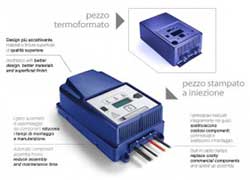
TECHNOLOGIES FOR MOULDING PLASTIC: THERMOFORMING OR INJECTION?
Injection moulding
The most widely used method for mass producing plastic objects is injection moulding. This is done using special presses which melt the plastic granules and inject it at high speed and pressure into the moulds where the polymer cools and hardens to the required shape. Injection moulding is used to process both thermoplastics and thermosetting polymers.
Sheet thermoforming
Thermoforming is a technique used for moulding heated plastic sheets. The product is created by moulding a sheet of pre-heated plastic over an aluminium mould. The plastic sheet, heated to make it pliable, is inflated like a balloon over the mould then, thanks to a strong vacuum created between the surface of the mould and the plastic sheet, it is laid over the mould where it replicates its shape and geometry. The strong points of sheet thermoforming, one of the solutions we offer our clients, lies in its production simplicity and the low investments needed for mass production.
Opting for injection moulding becomes essential when a product has to be manufactured on a very large scale. In fact, this is the only way to reduce costs and improve the quality and aesthetics of the product, ensuring the manufacturing company upholds an image of maximum professionalism.